Engineering Manager - Bridgeport, CT
UNITED STATES • FIELD AREA (corporate or plant) • FULL-TIME
Position Summary
The Engineering Manager implements, coordinates and performs the engineering support functions for plant operations and maintenance. Provides engineering support for safety and environmental performance and compliance, as well as compliance with contracts at the plant (generation, steam, wheeling and raw materials.) Provides technical support for daily operations, plant improvements, process improvements, and analysis of plant breakdowns and recommendation of corrective action. This includes project planning and execution (Capital and Major Maintenance), vendor and contractor oversight, as well as providing guidance and support for plant programs using predictive and preventive maintenance techniques. Act as technical contact point for insurance issues (fire/boiler, property and machinery). Responsible for overall plant engineering function and IT support.
Major Duties & Responsibilities
1. Department Head. Establish goals and objectives for the engineering group and organization of the various functions in the department with defined areas of responsibility and performance standards. Main departmental functions are as follows:
i. Engineering
ii. Plant Performance
iii. Operations and Maintenance Support
iv. Safety & Environmental Compliance Support
v. IT Support (includes DCS)
2. Ensure the development, implementation and evaluation of plant specific performance monitoring related to the following:
i. Availability Improvements
ii. Thermal Efficiency
3. Manage Plant Improvements/Capital Process. Compile all necessary data, investigate viable alternatives and make economic evaluations related to plant equipment and/or procedures modifications to ensure improved plant safety, availability, efficiency and environmental performance. Assist in the investigation of plant problems, incidents, accidents and unusual events and provide analysis, recommendations, reports and follow-up plans as required. Leads the plant’s configuration (management of change) process.
4. Implements and maintain a tracking system for plant issues that impact safety, environmental compliance, equipment condition, budget or generation.
5. Utilize tools and analysis techniques to identify developing equipment issues that might cause future forced outages or risks to personnel. Provide assistance in the development of preventative maintenance and scheduled maintenance activities.
6. Evaluate equipment failures and assist with Root Cause Analysis to prevent recurrence. Assist in the investigation of plant problems, incidents, accidents, and unusual events, and provide analyses, recommendations, reports, and appropriate follow-up plans.
7. Maintain and update the plant drawing files and files on equipment, testing, unit availability, generation and downtime statistics, thermal performance, DCS configuration and water chemistry.
8. Direct and control engineering expenditures to remain within budget guidelines. Provide relevant input to the budgetary process.
9. Provide necessary technical support in the preparation of bid specifications, evaluation of vendor/contractor bid proposals and monitoring of contractor work performance to assure contract compliance.
10. Assure IT Administration (including DCS) through which repairs, modifications and software changes are completed safely and without impacting unit operation.
11. Interface with and support the Administration, Operation, Maintenance, Environmental Health and Safety departments in achieving their goals and objectives. Provide technical input as required.
12. The assignments will involve coordination with Corporate Engineering, external contact with maintenance and engineering firms to discuss field changes, manufacturer sales representatives and service personnel and vendors to discuss new or modifications to existing equipment, resolve problems and exchange information. Has frequent internal contact with various plant personnel including shift supervisors, technicians and plant operations and maintenance personnel, to resolve problems, provide technical support and exchange information.
13. Other duties as assigned.
14. Follow all safety/environmental policies, procedures, and rules and participate in training. Promote the Company’s highest value, EH&S and NERC Compliance through actions and conduct and positively affects morale.
Education/Experience Required
1. A bachelor’s degree in engineering, or equivalent, plus a minimum of ten (10) years relevant power plant-related experience required.
2. A thorough, demonstrated understanding of power plant operations, including a working knowledge of the operations and maintenance components of the plant. A proficient knowledge of computer and control systems is needed. Knowledge of chemistry as related to power plant operations and water treatment programs. Understand budgets, bid proposals and contract evaluation and basic accounting principles. Knowledge of chemistry, physics, engineering and plant operations is beneficial for this job.
3. An ability to plan, coordinate and direct varied programs and tasks directly involved with the engineering component of the plant but directly influencing the entire plant operation. Analyze and interpret data to make sound professional judgments and recommendations. An ability to manage and motivate others and deal persuasively with all other managers and plant employees.
4. At least 5 years’ experience supervising technical, supervisory and administrative personnel required. Strong leadership and motivational skills required.
5. Licenses - Professional Engineering license in the state of Connecticut, not required, but strongly encouraged.
6. Must be able to read, write, speak and understand English.
7. Physical Requirements:
Requirements Physical Demands
Reaching/Pulling/Shoving Minimal
Bending/Stooping/Kneeling Frequent
Sight Acuity Near Frequent
Sight Acuity Far Frequent
Sight Depth Acuity Frequent
Sight Color Acuity Frequent
Talking (Loud and/or Clear) Moderate
Hearing Frequent
Heavy Lifting (>50 pounds) Minimal
Medium Lift (<50 pounds) Minimal
8. Additional Requirements:
i. Must have a valid driver’s license
ii. Occasional overnight travel is required
iii. Must be physically able to transit plant facilities, stairways and elevated platforms
iv. Must be able to work in a standard office environment and operate a computer and other office equipment
9. Working Conditions - Incumbent may be required to work in conditions where hazardous material and toxic fumes could be present. Additionally, incumbent will be exposed to areas of high heat, loud noise, steam, combustible gases, rotating machinery and other conditions normally encountered in an operating generation facility
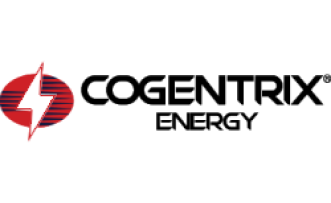
13860 Ballantyne Corporate Place, Suite 300, Charlotte, NC 28277
careers@cogentrix.com
704-525-2720
www.cogentrix.com
© Copyright 2023 Cogentrix Energy Power Management, LLC ALL Rights Reserved.